CASE STUDY / Goodridge Ltd
Cobwebb Document Management helped streamline Goodridge Ltd's global manufacturing operations.
INDUSTRY: Manufacturing
ERP SYSTEMS: System21 and XA
SOLUTION: Cobwebb Document Management / CPPD
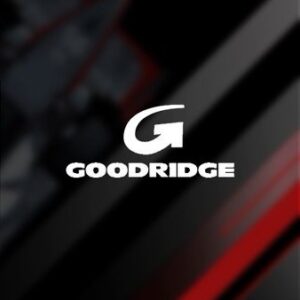
THE BACKGROUND
Founded in 1969, Goodridge has grown from a small unit in the Devon market town of Totnes, UK, to a global organisation, now manufacturing in ten facilities spread across nine countries. Goodridge manufactures and supplies fluid transfer assemblies, hose and fittings to world leading racing teams; competing in four wheel and two wheel categories.
Goodridge supplies customers around the world with a unique combination of design, innovation, reliability and outstanding service. They are always looking for continuous improvement, accelerating their business and providing excellent customer service.
THE CHALLENGE
Goodridge had been using a Windows based Output Management solution since 2016 and although the business had experienced some issues with the stability of the application, it was meeting requirements. This changed in 2019 when Goodridge moved System21 to the cloud and to a new datacenter in the US. Their Windows server remained in the UK and this new setup had a hugely negative impact on the performance of their Output Management application. It was now taking up to 5 minutes to output labels and some forms were taking more than an hour to print. Paul Butterworth, Goodridge Director of IT, needed to find a solution to this problem ASAP.
After exploring a number of options, Goodridge was introduced to Cobwebb Communications via Infor. With many years experience in migrating customers from Windows based output management solutions, Cobwebb was able to quickly assess the requirements and present a clear route forward to Goodridge.